How Strong Are Airplane Windows
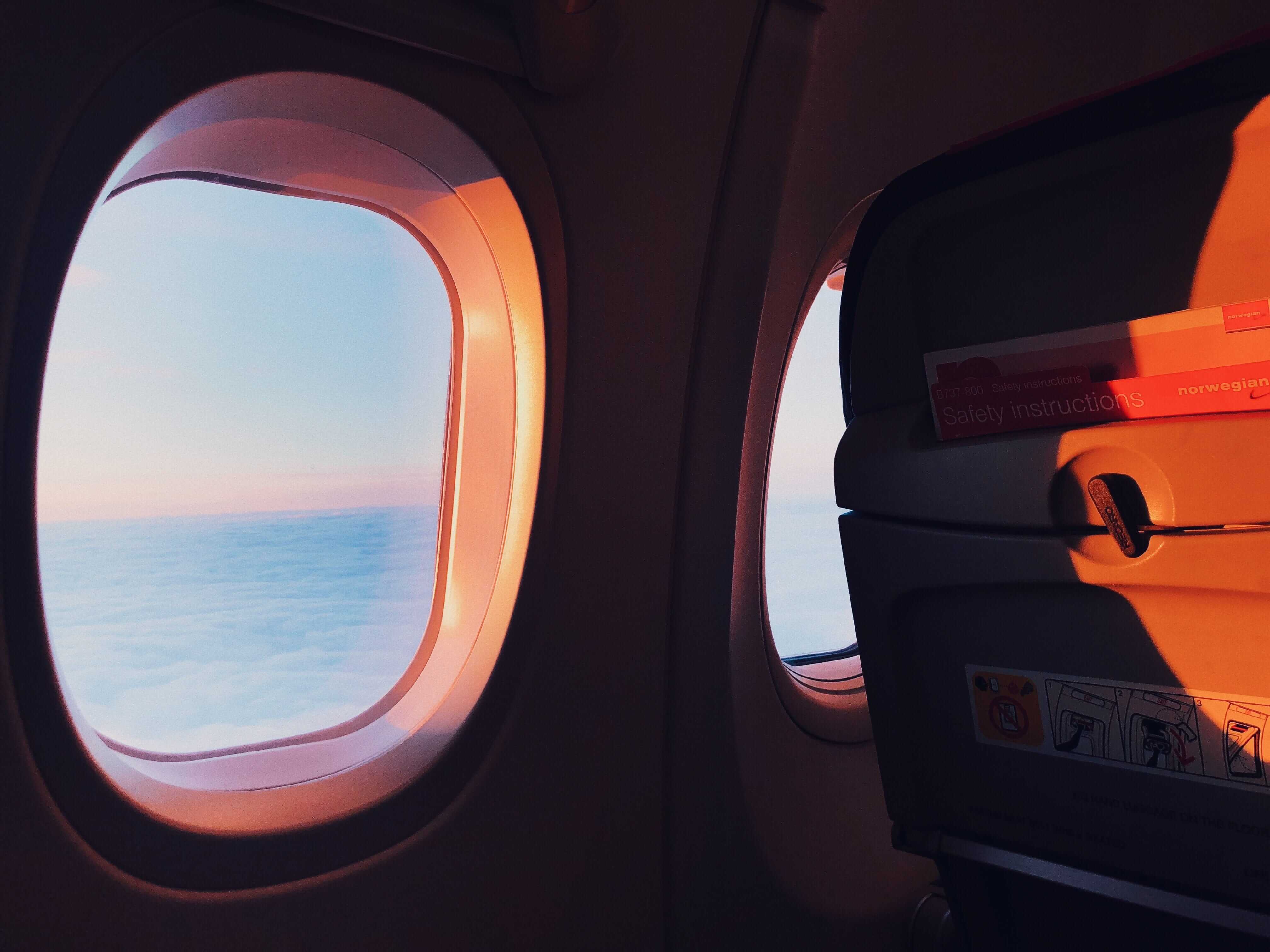
Introduction
Welcome aboard! If you’re a frequent traveler or preparing for your first flight, you might have wondered just how strong those airplane windows are. After all, they have to withstand the pressures of high altitudes, extreme temperatures, and turbulence. In this article, we will delve into the fascinating world of aircraft windows, exploring their strength and the materials used in their construction.
While sitting by the window, you may have marveled at the breathtaking views or perhaps experienced a few butterflies during takeoff or landing. But have you ever stopped to consider the incredible engineering behind these transparent barriers?
Aircraft windows serve a critical purpose beyond just offering passengers a view of the world below. They ensure the integrity of the cabin, protect against wind and noise, and provide an essential source of natural light. Given these responsibilities, it’s no wonder that aircraft windows need to be incredibly robust.
From the moment you step onto the plane, you can trust that the windows have undergone rigorous testing and adhere to strict safety regulations. Aircraft window design and construction have come a long way since the early days of aviation, and today’s windows are built to withstand the toughest conditions.
Join us on this journey as we explore the science and technology behind airplane windows. We’ll investigate the materials used, the testing and certification processes, and even delve into famous incidents involving window failures. Along the way, we’ll also discover the advancements and future developments in aircraft window technology.
So fasten your seatbelt and get ready to learn everything you’ve ever wanted to know about the strength of airplane windows. After all, knowledge is the key to peace of mind during your flights.
Understanding Aircraft Window Strength
When it comes to aircraft window strength, there are several factors at play. To understand how these windows are designed to withstand extreme conditions, let’s explore the key components that contribute to their robustness.
One crucial aspect of window strength is the capability to withstand the pressure differential between the inside and the outside of the aircraft. As an aircraft climbs to high altitudes, the cabin pressure decreases while the external atmospheric pressure decreases even more rapidly. This means that the windows must bear the immense pressure difference without compromising the integrity of the cabin.
The second factor is the ability to endure rapid changes in temperature during flight. As planes reach cruising altitudes of 35,000 feet or more, the outside temperature can plummet to -50 degrees Celsius (-58 degrees Fahrenheit) or even colder. Meanwhile, the inside of the cabin remains at a more comfortable temperature. This drastic temperature difference places additional stress on the windows, requiring them to handle thermal expansion and contraction without cracking or breaking.
Furthermore, aircraft windows must be able to withstand the forces of turbulence. Turbulence refers to the sudden changes in airflow that can occur during a flight. When the aircraft encounters turbulent conditions, the windows may experience vibrations and flexing. To ensure passenger safety and prevent any structural damage, the windows are designed to absorb these forces and maintain their structural integrity.
The materials used in aircraft window construction play a critical role in determining the strength of the windows. In the past, windows were made primarily of acrylic materials, but modern aircraft windows consist of multiple layers of specialized materials. These layers include a protective external pane, a middle pane made of a strong composite material, and an inner pane that acts as a barrier against the cabin pressure. This multi-layer construction provides additional strength and enhances the overall resilience of the windows.
Now that we have a basic understanding of aircraft window strength, let’s explore the materials used in their construction and the rigorous testing and certification processes they undergo to ensure passenger safety.
Materials Used in Aircraft Windows
The materials used in aircraft windows are carefully chosen to withstand the demanding conditions of flight while providing optimal visibility for passengers. Modern aircraft windows are typically made of a combination of several materials that work together to ensure strength, durability, and safety.
The external layer of the aircraft window, also known as the “scratch pane,” is made of materials like acrylic or polycarbonate. These materials are chosen for their excellent transparency and resistance to scratches, ensuring that the window remains clear and unobstructed despite exposure to harsh external elements.
Beneath the scratch pane lies the middle pane, which is usually made of a composite material such as glass-fiber-reinforced epoxy or polycarbonate. This layer provides structural integrity and contributes to the overall strength of the window. The composite material used is lightweight yet robust, allowing the window to withstand the extreme pressure differentials and temperature fluctuations experienced during flight.
The innermost layer of the aircraft window, known as the “pressure pane,” is typically made of chemically toughened glass. This layer is specifically designed to withstand the cabin pressure while maintaining transparency. Chemically toughened glass is highly resistant to shattering, ensuring that even in the unlikely event of a crack or break, the glass will not splinter or pose a risk to passengers.
Additionally, between each layer of the window, there are bonding materials and adhesives that help to keep the layers securely together. These bonding materials are carefully selected to provide a strong bond while allowing for the necessary flexing and movement of the window during flight.
The combination of these materials and their specific properties ensures that aircraft windows can withstand the pressure differentials, extreme temperatures, and potential impacts that they may encounter during flight. However, it’s important to note that despite their strength, aircraft windows are not entirely indestructible and can still be damaged by severe impacts or other extraordinary circumstances.
Now that we understand the materials used in aircraft windows, let’s delve into the rigorous testing and certification processes that these windows undergo to ensure their safety and reliability.
Testing and Certification of Aircraft Windows
Before an aircraft window makes its way onto a commercial airplane, it undergoes a series of rigorous testing and certification processes to ensure its strength, durability, and ability to withstand the demanding conditions of flight.
First and foremost, each window design undergoes extensive computer simulations and modeling to assess its structural integrity. These simulations analyze factors such as pressure differentials, temperature fluctuations, and turbulence forces to ensure the window design can withstand these stresses without compromising safety.
Once the design is deemed satisfactory, physical testing commences. One of the primary tests conducted on aircraft windows is the pressure test. The window is exposed to varying pressures to simulate the cabin pressure at different altitudes. This test ensures that the window can withstand these pressure differentials without deformation or failure.
The windows are also subjected to temperature testing. They are exposed to extreme temperatures found at high altitudes, as well as rapid changes in temperature, to verify their ability to handle thermal expansion and contraction without cracking or compromising their structural integrity.
Impact resistance testing is another crucial step in the certification process. The windows are subjected to impacts from objects such as bird strikes or other foreign debris to assess their ability to withstand such occurrences without shattering or compromising the safety of passengers.
Additionally, aircraft windows undergo testing for resistance to UV radiation, which can degrade materials over time. Ensuring the windows remain resistant to UV exposure helps maintain their optical clarity and longevity.
Throughout the testing process, rigorous inspections and evaluations are conducted to assess the performance and structural integrity of the windows. These evaluations involve visual inspections, measurements, and non-destructive tests to identify any potential issues or defects.
Once a specific window design successfully passes all the necessary tests, it receives certification from aviation regulatory authorities, such as the Federal Aviation Administration (FAA) in the United States or the European Union Aviation Safety Agency (EASA) in Europe. This certification ensures that the window meets the stringent safety standards required for commercial aviation.
It’s worth noting that even after certification, periodic inspections and maintenance procedures are carried out to monitor the condition of the windows throughout their lifespan. This proactive approach helps identify any signs of wear, damage, or other issues that may necessitate repairs or replacement.
By subjecting aircraft windows to thorough testing and certification processes, manufacturers and regulatory authorities ensure that these vital components meet the highest standards of safety and reliability, providing passengers with peace of mind during their flights.
Famous Incidents Involving Aircraft Window Failures
While aircraft window failures are rare, there have been a few notable incidents that have highlighted the importance of window strength and safety in aviation. These incidents serve as reminders of the constant efforts made by the industry to enhance window construction and maintenance procedures.
One such incident occurred in April 2018 when a Southwest Airlines flight experienced an engine failure, resulting in an uncontained engine explosion. The explosion caused debris to puncture one of the aircraft’s windows, leading to cabin depressurization. Tragically, one passenger lost their life due to the incident. This incident prompted a thorough review of engine and window designs, as well as enhanced inspections and maintenance protocols.
Another well-known incident dates back to 1988 when a Boeing 747-121, operating as TWA Flight 841, experienced a sudden loss of cabin pressure. Investigation revealed that a failure in one of the forward windows caused the rapid decompression. The incident underscored the importance of window inspections and maintenance to prevent such catastrophic events.
There have also been incidents where aircraft windows have shattered without causing immediate danger to passengers. In 2011, a Qantas Airbus A380 flight from Singapore to Sydney experienced an uncontained engine failure that resulted in several windows being shattered. Fortunately, the aircraft was able to land safely, and no injuries were reported. The incident sparked discussions around engine design and the potential risks associated with shattered windows.
These incidents have spurred the aviation industry to continuously improve window construction, maintenance procedures, and safety protocols. Manufacturers have implemented enhanced window designs and materials that are more resistant to impacts, changes in pressure, and extreme temperatures. Additionally, strict inspection and maintenance programs have been put in place to identify and address any potential window issues before they compromise passenger safety.
It is important to note that despite these incidents, flying remains one of the safest modes of transportation. The industry’s commitment to continuous improvement and learning from past experiences helps ensure that window failures are extremely rare occurrences. Millions of flights safely take to the skies each year, thanks in part to the lessons learned from these incidents.
In the next section, we will explore the advancements and future developments in aircraft window technology as the industry strives to enhance passenger safety and comfort.
Improvements and Future Developments in Aircraft Window Technology
The aviation industry is continuously researching and developing new technologies to improve aircraft window strength, safety, and passenger comfort. As new materials and innovations emerge, we can expect to see exciting advancements in aircraft window technology.
One area of improvement is the development of stronger and lighter window materials. Manufacturers are exploring advanced composite materials, such as carbon fiber-reinforced polymers, that offer enhanced strength while reducing the weight of the windows. This not only improves fuel efficiency but also allows for larger windows, offering passengers a better view of the outside world.
Another focus is on incorporating smart technologies into aircraft windows. This includes the integration of sensors and embedded systems that can monitor the condition of the windows in real-time. These sensors can detect early signs of damage or stress, allowing for proactive maintenance and preventing potential failures before they occur.
Advancements are also being made in window coatings and films to improve visibility and reduce glare. These coatings can enhance optical clarity, reduce the effects of UV radiation, and provide better insulation against heat and cold. These advancements not only improve the passenger experience but also contribute to the overall energy efficiency of the aircraft.
Furthermore, the integration of augmented reality (AR) technology is being explored to enhance the in-flight experience for passengers. AR-enabled windows could provide real-time information about the flight, landmarks, and points of interest, offering a more engaging and informative journey.
In terms of safety, manufacturers are working on developing windows that can automatically darken in the event of a sudden light intensity change, such as a lightning strike. This technology, known as electrochromic dimming, can help protect passengers’ eyes from the bright flash while maintaining visibility through the window.
Looking to the future, there is ongoing research into the development of self-healing materials for aircraft windows. These materials have the ability to repair minor damage, such as scratches or small cracks, without compromising the structural integrity of the window. This technology could significantly reduce maintenance costs and enhance the lifespan of the windows.
It’s worth noting that while these advancements show great promise, they require extensive testing and regulatory approval before implementation. Safety and reliability remain the utmost priority in the aviation industry, and any new technology must undergo rigorous scrutiny to ensure it meets the strict standards set forth by aviation authorities.
As the aviation industry continues to innovate and improve aircraft window technology, passengers can look forward to safer, more comfortable, and visually captivating flying experiences. From stronger and lighter materials to advanced smart features, these advancements will further enhance the already remarkable world of aviation.
Conclusion
Aircraft windows are remarkable engineering marvels that have evolved significantly over the years. From withstanding extreme pressure differentials and temperature fluctuations to enduring the forces of turbulence, these windows play a crucial role in ensuring passenger safety and comfort during flight.
Through the meticulous selection of materials, rigorous testing, and adherence to stringent certification processes, aircraft windows are designed to withstand the harshest conditions of flight. The use of advanced composite materials, smart technologies, and coatings enhances their strength, durability, and performance.
While rare incidents of window failures have occurred in the past, they have led to significant advancements and improvements in window design and maintenance protocols. Manufacturers and regulatory authorities continuously strive to enhance window technology and incorporate innovative features that further enhance passenger safety and comfort.
The future of aircraft window technology holds promise, with ongoing research and development focused on stronger and lighter materials, smart features, and self-healing capabilities. These advancements will enhance the passenger experience, improve fuel efficiency, and contribute to the overall sustainability of air travel.
As you look out of an airplane window on your next flight, you can now appreciate the complexity and strength of these transparent barriers. From the materials used to the testing and certification processes they undergo, aircraft windows exemplify the dedication of the aviation industry to providing safe and enjoyable air travel.
So, the next time you find yourself gazing at the clouds or capturing a breathtaking view from your airplane window, remember the remarkable engineering behind those windows and the ongoing efforts to ensure your flight is as safe and comfortable as possible.