How Plastic Bottle Is Made
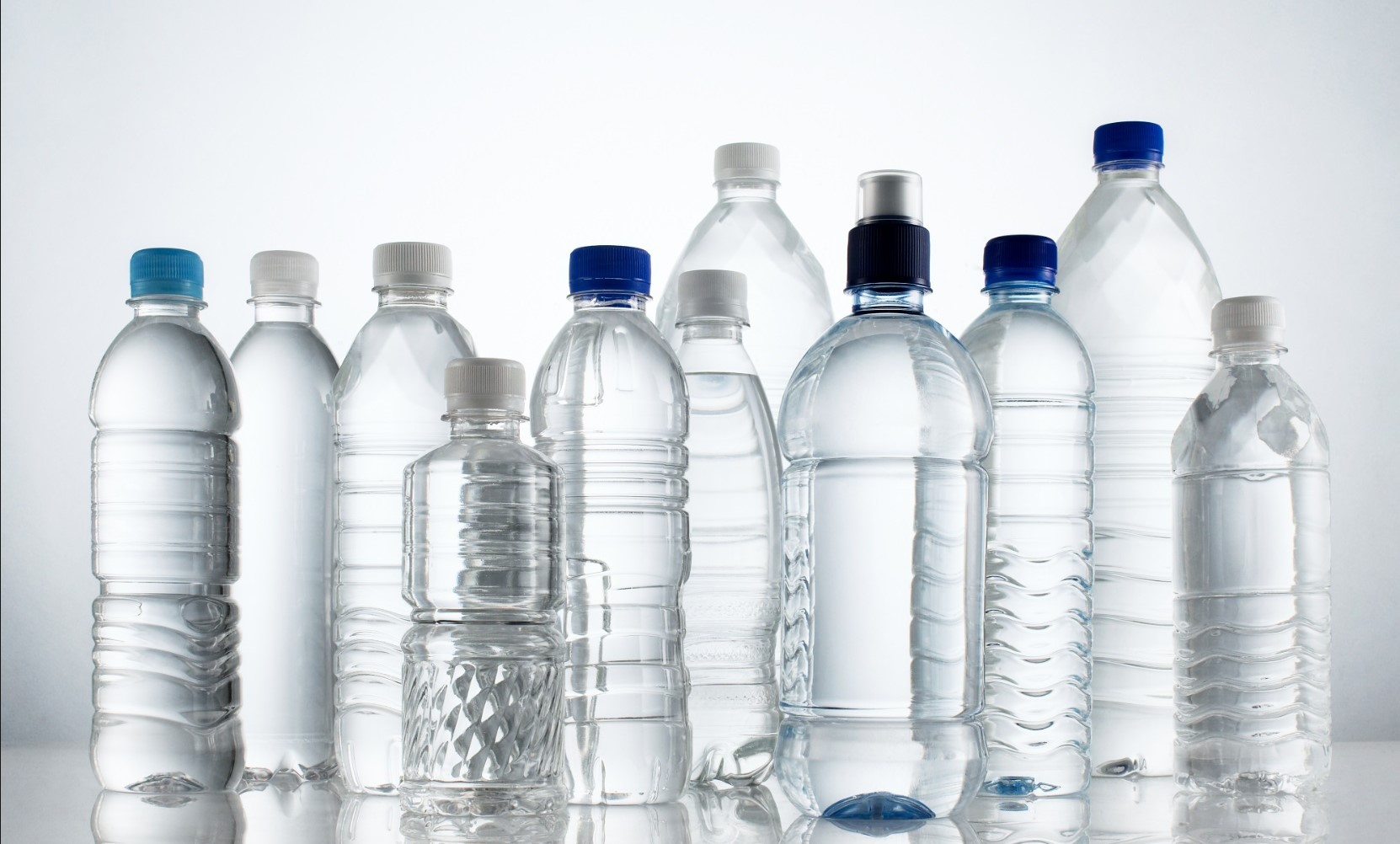
Introduction
Plastic bottles have become an indispensable part of our everyday lives. They are used for storing various liquids like water, beverages, cleaning products, and more. Have you ever wondered how these plastic bottles are made? The process of manufacturing plastic bottles involves several steps, each contributing to the final product’s quality and durability.
In this article, we will delve into the fascinating journey of a plastic bottle, from the selection of raw materials to the final packaging and distribution. Understanding this process will give us a deeper appreciation for the convenience and reliability that plastic bottles offer.
Plastic bottles are made from a type of plastic called polyethylene terephthalate (PET). PET is a lightweight, durable, and versatile material that is ideal for producing bottles with various shapes and sizes. The manufacturing process for plastic bottles typically involves high-tech machinery and a series of carefully orchestrated steps.
Let’s take a closer look at each stage of the manufacturing process to understand how plastic bottles are brought to life.
Manufacturing Process
The manufacturing process of plastic bottles is a complex and precise operation that requires advanced machinery and skilled technicians. It involves several crucial steps, including raw material selection, plastic resin preparation, extrusion, injection molding, blow molding, labeling and printing, quality control, and packaging and distribution.
Each step in the process plays a vital role in ensuring the final product’s quality, strength, and functionality. Let’s explore each of these steps in detail:
- Raw Material Selection: The first step in making plastic bottles is selecting the right raw material. Typically, high-quality PET resin is chosen because of its durability, clarity, and recyclability. The resin is carefully inspected and tested to ensure it meets the desired specifications.
- Plastic Resin Preparation: Once the raw material is selected, it undergoes a process called polymerization. In this process, the PET resin is heated and melted to form a liquid state. This liquid resin is then cooled and cut into small pellets, ready for the next stage of production.
- Extrusion: The extrusion process involves feeding the PET pellets into a hopper, which then transfers them to an extruder. Inside the extruder, the pellets are melted and pushed through a die, resulting in a long, continuous tube of molten plastic. This tube is then cooled and solidified.
- Injection Molding: Injection molding is used to create plastic bottles with intricate shapes and features. The cooled and solidified tube from the extrusion process is cut into small pellets and fed into an injection molding machine. The machine heats the pellets until they melt and injects the molten plastic into a mold. The mold is then cooled, and the plastic solidifies, forming the shape of the bottle.
- Blow Molding: For producing bottles with hollow interiors, the blow molding process is used. After injection molding, the bottles are transferred to a blow molding machine. The machine uses pressurized air to inflate the molten plastic, causing it to conform to the shape of the mold. Once the plastic has cooled and hardened, the mold is opened, and the finished bottle is ejected.
- Labeling and Printing: Once the bottles have been molded, they are ready for labeling and printing. Labels with product information, logos, and other designs are applied to the bottles using automated labeling machines. Additionally, printing techniques such as screen printing or digital printing are used to add intricate designs or branding.
- Quality Control: Throughout the entire manufacturing process, strict quality control measures are implemented to ensure that the bottles meet industry standards and customer expectations. Quality control professionals inspect the bottles for defects, such as cracks, deformities, or inconsistencies in color or size. This step helps to ensure that only high-quality bottles make it to the market.
- Packaging and Distribution: Once the bottles have passed quality control, they are packaged and prepared for distribution. This includes grouping the bottles into cartons or crates, stacking and shrink-wrapping them for transportation, and labeling the packages for easy identification. The packaged bottles are then sent to distributors, retailers, or directly to consumers.
The manufacturing process of plastic bottles exemplifies precision and efficiency. By following these meticulous steps, manufacturers can create bottles that are not only visually appealing but also functional and durable.
Step 1: Raw Material Selection
In the process of manufacturing plastic bottles, selecting the right raw material is crucial to ensure the quality, durability, and sustainability of the final product. The most commonly used material for plastic bottles is polyethylene terephthalate (PET). PET is valued for its lightweight nature, excellent barrier properties, and high clarity, making it an ideal choice for packaging various liquids.
The first consideration in raw material selection is the quality of the PET resin. Manufacturers carefully evaluate different resin suppliers and their products to ensure they meet the required specifications. This evaluation includes factors such as resin purity, molecular weight distribution, and color consistency.
Resin purity is critical as impurities can compromise the physical properties and performance of the plastic bottles. High-quality PET resin should have minimal levels of contaminants, such as moisture, metal ions, and other foreign particles.
The molecular weight of the resin determines the strength and stiffness of the plastic bottles. A carefully controlled molecular weight distribution ensures uniformity throughout the material, resulting in consistent bottle performance and resistance to stress and impact.
Color consistency is also essential, especially for clear plastic bottles. Manufacturers aim for a resin that provides excellent clarity, allowing the contents of the bottle to be easily visible. Consistent color throughout the batch ensures that the bottles have an attractive and uniform appearance.
Another important aspect of raw material selection is considering the recyclability of the PET resin. As sustainability becomes increasingly important, manufacturers strive to use resins that are easily recyclable. PET is a highly recyclable material and can be transformed into various products, including new plastic bottles.
Furthermore, the raw material selection process takes into account factors such as cost, availability, and regulatory compliance. Manufacturers assess the cost-efficiency of different resin suppliers while ensuring a reliable and consistent supply chain. Compliance with industry regulations and standards, such as FDA approval for food-grade bottles, is also a critical consideration.
Overall, the careful selection of raw materials sets the foundation for producing high-quality plastic bottles. By choosing the right PET resin, manufacturers can ensure the bottles’ performance, aesthetics, and sustainability, meeting the demands of consumers and adhering to industry standards.
Step 2: Plastic Resin Preparation
Once the raw material selection is complete, the next step in manufacturing plastic bottles is the preparation of the plastic resin. The chosen raw material, typically polyethylene terephthalate (PET), undergoes a process called polymerization to transform it into a suitable form for bottle production.
The polymerization process begins by heating and melting the PET resin. This is typically done in a controlled environment to ensure precise temperature and time settings. The heating process converts the raw material into a liquid state, allowing it to be manipulated and shaped.
After the resin is melted, it is then cooled and cut into small pellets, commonly known as “preforms.” These preforms serve as the building blocks for the subsequent stages of plastic bottle production.
Preparing the plastic resin involves ensuring its composition and characteristics meet the desired specifications. The resin should have a consistent molecular weight distribution to ensure the final bottles exhibit consistent strength, flexibility, and resistance to stress.
In addition, any impurities or contaminants present in the resin, such as moisture, are carefully removed during the resin preparation process. This helps maintain the integrity and quality of the final product.
The plastic resin preparation phase also provides an opportunity to add colorants or additives to the PET resin, if desired. Colorants can be mixed with the molten resin to create bottles with different hues or translucent effects. Additives, such as UV stabilizers or oxygen scavengers, can be incorporated to enhance the bottle’s functionality and longevity.
Ensuring the plastic resin is properly prepared is crucial for achieving consistent and high-quality plastic bottles. The melted and solidified preforms preserve the desired physical properties of the resin and are ready for the subsequent stages of the manufacturing process.
By carefully preparing the plastic resin, manufacturers can create preforms that are uniform in composition, free from impurities, and capable of being efficiently molded into the final bottle shapes. This step sets the foundation for the subsequent steps in the manufacturing process and contributes to the overall quality and performance of the plastic bottles.
Step 3: Extrusion
After the plastic resin preparation, the next step in manufacturing plastic bottles is the extrusion process. Extrusion is a method used to shape the plastic material into a continuous tube or profile, which will serve as the basis for forming the bottles.
The extrusion process starts by feeding the prepared plastic resin, in the form of small pellets or preforms, into a hopper. From the hopper, the resin is transported to an extruder, which is a machine equipped with a screw mechanism. The screw rotates and pushes the resin forward, gradually melting it under controlled temperature and pressure.
As the resin advances through the extruder, it is subject to high heat, which liquefies it completely. The molten plastic passes through a specially shaped tool called a die, which determines the outer shape of the tube or profile. The die has an opening that matches the desired shape and size of the plastic bottle.
As the molten plastic is forced through the die, it takes on the shape of the opening and emerges as a continuous tube of plastic. This tube is then cooled, often through the use of cooling fans or water sprays, causing it to solidify and maintain its new shape.
The extrusion process allows for the creation of different tube sizes and shapes, accommodating a wide range of bottle designs. By using different dies and adjusting the speed at which the plastic is extruded, manufacturers can produce tubes of various diameters and wall thicknesses.
Furthermore, during the extrusion process, it is possible to incorporate additional features into the plastic tube, such as handles or threaded necks. These features can be added by using specialized tooling or modifying the extrusion equipment.
Once the extrusion process is complete, the continuous tube of plastic is cut into individual sections known as parisons. These parisons will serve as the starting point for the subsequent stages of bottle production, such as injection molding or blow molding.
The extrusion process is a critical step in the manufacturing of plastic bottles as it provides the foundation for shaping the bottles’ final form. It allows for flexibility in design and ensures the consistency of the tube’s dimensions and shape, setting the stage for creating high-quality bottles.
Step 4: Injection Molding
Injection molding is a widely used method in the production of plastic bottles. This step involves injecting molten plastic material into a mold to shape it into the desired bottle form. Injection molding allows for precise control over bottle design, enabling the creation of intricate shapes and features.
The process of injection molding starts with the preparation of the plastic material. The extruded parisons from the previous step are cut into smaller pieces called preforms. These preforms are loaded into an injection molding machine’s hopper, where they are heated to their melting point.
Inside the injection molding machine, the preforms are fed into a heated barrel and subjected to high temperatures, causing them to melt completely. The molten plastic is then injected under high pressure into a mold cavity, shaped as per the desired bottle design.
Once the molten plastic is injected into the mold, it rapidly cools and solidifies, taking on the shape of the mold. The cooling process is aided by cooling channels or systems within the mold. The mold itself is typically made of durable materials, like steel or aluminum, to withstand the heat and pressure.
After the plastic has cooled and hardened inside the mold, the mold is opened, and the newly formed plastic bottle is ejected. The bottles are then trimmed and inspected for any defects or imperfections.
Injection molding offers several advantages in the production of plastic bottles. It allows for high production volumes with consistent quality and precise control over bottle dimensions and features. The process is highly automated and can be fine-tuned to meet specific requirements.
The versatility of injection molding enables the creation of bottles with intricate designs, such as ergonomic grips, intricate handles, or unique neck shapes. It also allows for the incorporation of threads or seals, ensuring the bottles can be securely sealed with caps or lids.
Injection molding is particularly suitable for producing bottles in various sizes and shapes, ranging from small cosmetic containers to large beverage bottles. The process provides a cost-effective and efficient solution for large-scale production, meeting the demand for plastic bottles across various industries.
By utilizing injection molding, manufacturers can produce plastic bottles with consistent quality, precise dimensions, and the desired features, meeting the diverse needs of consumers and industries alike.
Step 5: Blow Molding
The blow molding process is a key step in the manufacturing of plastic bottles, especially for producing bottles with hollow interiors. This method allows for the creation of a wide range of bottle shapes and sizes, including those with unique curves or contoured designs.
The blow molding process begins with the heated parisons obtained from the extrusion or injection molding stage. These parisons are placed in a mold cavity, typically made from two halves, where they are clamped and secured in place.
Once the parisons are in position, a blow molding machine introduces pressurized air into the parison, forcing it to expand and conform to the shape of the mold. The pressurized air enters through a small opening in the mold, known as the blow pin, located at the center of the parison.
As the parison expands, the molten plastic material takes on the mold’s contours, creating the desired bottle shape. The mold walls help to maintain the shape as the plastic cools and solidifies. The cooling process can be accelerated through the use of cooling fans or water sprays within the mold.
Once the plastic has sufficiently cooled and hardened, the mold is opened, and the newly formed plastic bottle is released. The excess plastic material, known as flash, is trimmed off to achieve a clean and finished appearance.
The blow molding process offers significant advantages in terms of versatility and cost-effectiveness. It allows for the production of bottles with consistent wall thickness, ensuring strength and durability. The process can create bottles in various sizes and shapes, accommodating a wide range of packaging needs.
Additionally, blow molding enables the integration of special features within the bottle design, such as handles, spouts, or even multiple compartments for different contents. The process can also be used to produce bottles with different neck finishes, allowing for compatibility with various cap or closure types.
Blow molding is commonly used to manufacture bottles for beverages, personal care products, household chemicals, and other consumer goods. The process provides an efficient and cost-effective solution for producing large quantities of bottles with consistent quality and intricate designs.
By utilizing blow molding techniques, manufacturers can produce lightweight, durable, and visually appealing plastic bottles that meet the different demands of consumers and industries.
Step 6: Labeling and Printing
Once the plastic bottles have been molded, the next step in the manufacturing process is labeling and printing. This step adds the finishing touches to the bottles, providing important information, branding, and visual appeal.
Labeling involves applying a label onto the surface of the bottle. These labels typically include important details such as product information, ingredients, usage instructions, and safety precautions. Labels can also serve as a way to showcase the brand logo or artwork, enhancing the overall aesthetics of the bottle.
The labeling process is often automated, using labeling machines that carefully apply the labels onto the bottles. These machines ensure precise placement and alignment of the labels, contributing to a professional and visually appealing final product.
In addition to labeling, the printing process allows for adding further designs or information directly onto the bottle’s surface. This can be done through various printing techniques, such as screen printing, pad printing, or digital printing.
Screen printing involves transferring ink through a mesh screen with a stencil onto the bottle surface. This technique allows for vibrant colors, intricate designs, and precise details. Pad printing, on the other hand, uses a silicone pad to pick up ink from an etched plate and transfer it onto the bottle’s surface.
Digital printing, a more modern and advanced method, utilizes specialized printers that directly apply ink onto the bottle in a digital format. This method allows for high-resolution images, customization, and quick turnaround times.
Labeling and printing serve multiple purposes beyond providing information and branding. They can also include features such as barcodes or QR codes, enabling easy tracking of products or providing interactive experiences for consumers.
The labeling and printing process adds value to the plastic bottles, making them visually appealing, informative, and market-ready. It contributes to building brand recognition, enhancing product visibility, and attracting consumers.
Furthermore, labeling and printing play a crucial role in compliance with regulatory requirements. For example, food-grade bottles must display specific information and adhere to certain labeling standards.
By incorporating efficient and accurate labeling and printing processes, manufacturers can ensure that their plastic bottles are well-presented, informative, and align with industry standards, meeting the expectations and preferences of consumers.
Step 7: Quality Control
Quality control is a critical step in the manufacturing process of plastic bottles. It ensures that the final products meet specified standards and requirements in terms of durability, performance, and appearance.
Throughout the production process, various quality control measures are implemented to identify and address any defects or inconsistencies. These measures include both automated systems and human inspection to ensure the highest level of quality.
One of the primary quality control checks is performed during the molding process. The bottles undergo a thorough inspection for any visible defects, such as cracks, warping, or irregularities in shape or size. This ensures that only bottles of the highest quality proceed to the next stages of production.
Additionally, sample bottles are routinely taken from the production line for further testing. These tests may include physical and mechanical evaluations to assess the bottles’ strength, integrity, and resistance to impact, pressure, or leakage.
Moreover, quality control measures include checks on the accuracy and consistency of labeling and printing. This ensures that the information displayed on the bottle is correct, the artwork is aligned properly, and the print quality meets high standards.
Furthermore, manufacturers may perform tests to verify the bottle’s compatibility with specific products or environments. These tests can assess factors such as chemical resistance, temperature tolerance, and UV stability.
Quality control efforts extend beyond the manufacturing process. Finished bottles undergo a final inspection to identify any last-minute defects or imperfections before they are packaged and shipped. This step helps ensure that only flawless bottles reach the market.
Compliance with industry regulations and standards is also an essential aspect of quality control. For instance, manufacturers producing food-grade bottles must adhere to strict guidelines and demonstrate compliance with relevant agencies, such as the FDA, to ensure the bottles’ safety for consumers.
By implementing robust quality control measures, manufacturers can confidently deliver plastic bottles that meet or exceed customer expectations. This not only ensures product reliability but also contributes to consumer satisfaction and brand reputation.
Continuous improvement and ongoing monitoring of quality control processes are vital to adapt to evolving standards and maintain consistent product excellence throughout the production of plastic bottles.
Step 8: Packaging and Distribution
After the plastic bottles have successfully passed quality control, the next step in the manufacturing process is packaging and distribution. This step involves carefully packaging the bottles to ensure their protection during transit and preparing them for delivery to retailers, distributors, or customers.
The packaging stage begins by grouping the bottles into suitable quantities, considering factors such as bottle size, weight, and market demands. The bottles are often packed in cartons or crates to facilitate handling and transportation.
During the packaging process, attention is given to proper arrangement and secure stacking to prevent damage to the bottles. Packaging materials such as dividers, foam inserts, or cardboard partitions may be used to provide additional protection and prevent bottles from shifting or colliding.
To safeguard the bottles further, shrink-wrap may be applied to the entire package. This plastic film provides an extra layer of protection against moisture, dust, and potential tampering, ensuring the bottles remain in optimal condition until they reach their destination.
Before the packaged bottles are dispatched, labels or barcodes are affixed to the outside of the package for easy identification and tracking. These labels contain information such as the product name, quantity, batch or lot number, and sometimes specific handling instructions or warnings.
Once the bottles are adequately packaged and labeled, they are ready for distribution. Depending on the distribution channels and agreements in place, the bottles may be transported to retailers, distributors, or directly to consumers.
The distribution process involves arranging for the bottles’ transportation, whether it be by truck, ship, air, or a combination of these. Careful handling and transit conditions are essential to ensure the integrity of the packaged bottles, avoiding any potential damage or breakage during delivery.
Throughout the distribution process, manufacturers and distributors maintain close oversight to track and monitor the bottles’ progress. This allows for efficient logistics management, optimizing delivery times, and ensuring customer satisfaction.
Ultimately, packaging and distribution play a crucial role in bringing the finished plastic bottles to market. Proper packaging ensures the bottles arrive in pristine condition and ready for use. Effective distribution guarantees that the bottles reach their intended destinations efficiently and in a timely manner.
By paying attention to the packaging and distribution processes, manufacturers can uphold product quality, protect the bottles during transit, and ensure that customers receive their plastic bottles in excellent condition, ready for use or resale.
Conclusion
The manufacturing process of plastic bottles involves a meticulous series of steps, each playing a crucial role in creating high-quality, durable, and functional products. From the selection of raw materials to the packaging and distribution, every stage contributes to the final outcome.
The careful selection of the raw material, typically polyethylene terephthalate (PET), ensures that the bottles possess the desired properties of strength, clarity, and recyclability. The plastic resin is prepared through the polymerization process, resulting in molten resin that is shaped through extrusion or injection molding.
Extrusion forms the plastic material into continuous tubes, while injection molding allows for the creation of intricate bottle shapes. Blow molding is then used to produce bottles with hollow interiors, offering versatility in design and functionality.
Once the bottles take shape, they undergo labeling and printing, adding vital information and appealing visual designs. Quality control measures are implemented throughout the entire process to ensure that only flawless bottles make it to the market.
The bottles are carefully packaged to protect them during distribution, with labels and barcodes applied for easy identification and tracking. The bottles then move through the distribution channels, reaching retailers, distributors, or customers efficiently and intact.
In conclusion, the manufacturing of plastic bottles is a precise and comprehensive process that combines technology, quality control, and creativity. Manufacturers strive to create bottles that not only meet the functional needs of consumers but also cater to their aesthetic preferences and industry standards.
Understanding the journey of a plastic bottle from the selection of raw materials to its ultimate packaging and distribution allows us to appreciate the intricate work and attention to detail that goes into their creation. It also reminds us of the significance of sustainable practices, as recycling and environmentally friendly materials continue to shape the future of plastic bottle manufacturing.