How Long Does It Take To Build An Airplane
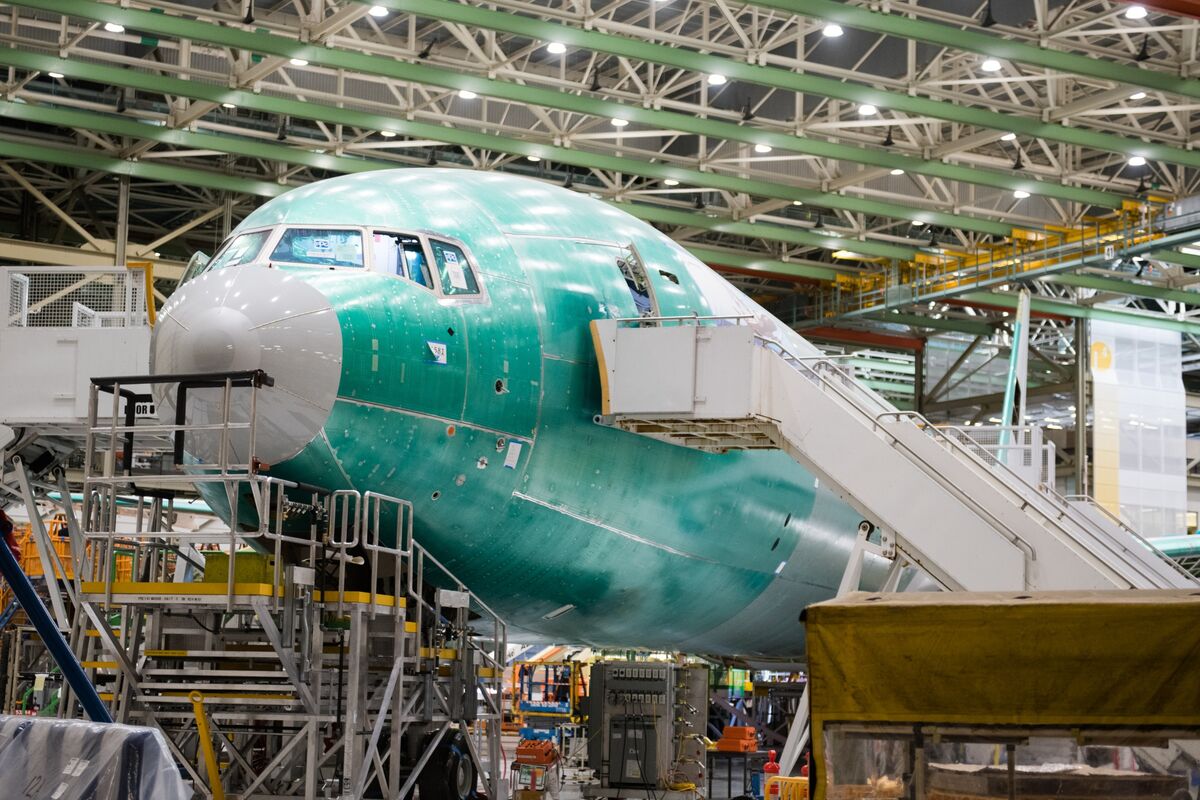
Introduction
Building an airplane is a complex and intricate process that requires meticulous planning, skilled labor, and adherence to stringent industry standards and regulations. From the initial design and planning stage to the final testing and certification, constructing an airplane involves numerous factors that impact the overall construction time.
However, it’s important to note that the time it takes to build an airplane can vary significantly depending on various factors, including the type of aircraft, the level of customization required, the efficiency of the manufacturer, and the collaboration with suppliers and contractors. In this article, we will explore the different stages of airplane construction and the factors that influence the timeline.
Before diving into the details, it’s crucial to emphasize that building an airplane is not a simple task. It requires a well-coordinated effort from a team of experts in various fields, including engineers, designers, mechanics, and technicians. Each stage of the construction process plays a vital role in ensuring the safety, reliability, and performance of the final product.
Whether it’s a small single-engine aircraft or a commercial airliner, the construction process involves a combination of art and science. Planes are not assembled overnight; rather, they undergo a step-by-step process that allows for meticulous inspection, testing, and verification before a plane is deemed airworthy.
In the following sections, we will delve deeper into the different factors that affect the construction time of an airplane. By understanding these factors, you will gain insight into the complexity of the process and the importance of each stage in delivering a safe and reliable aircraft.
Factors Affecting Construction Time
The construction time of an airplane can be influenced by a variety of factors. Understanding these factors can provide insight into why the time required to build an airplane can vary significantly. Here are some key factors that impact the construction time:
- Size and Complexity: The size and complexity of the airplane play a significant role in determining the construction time. Larger and more complex aircraft, such as commercial airliners or military jets, require more intricate designs, advanced manufacturing techniques, and thorough testing, all of which contribute to increased construction time.
- Level of Customization: If an aircraft is being customized to meet specific requirements or to incorporate optional features, the construction time will be affected. Customization may involve modifications to the interior, avionics systems, or even structural elements of the airplane, all of which require additional time and resources.
- Manufacturer’s Efficiency: The efficiency and experience of the aircraft manufacturer play a crucial role in determining the construction time. Established manufacturers with a streamlined production process, skilled workforce, and efficient supply chain management can significantly reduce the construction time compared to less experienced or less efficient manufacturers.
- Collaboration with Suppliers and Contractors: The collaboration and coordination with suppliers and contractors can impact the construction time. A well-established network of reliable suppliers and contractors who can deliver components and services on time and according to the required specifications is crucial for minimizing delays and ensuring a smooth construction process.
- Industry Standards and Regulations: Compliance with industry standards and regulations is an essential aspect of aircraft construction. The adherence to these standards ensures the safety and airworthiness of the aircraft. However, the stringent certification process and the need to comply with constantly evolving regulations can add time to the construction process.
These are just a few examples of the factors that can influence the construction time of an airplane. It’s important to note that these factors are interrelated, and a delay or change in one factor can have a cascading effect on the overall construction timeline. As such, skilled project management and effective communication between all stakeholders involved are critical to ensure a timely and successful completion of the aircraft construction process.
Design and Planning Stage
The design and planning stage is the initial phase of aircraft construction and sets the foundation for the entire process. This stage involves extensive research, conceptualization, and design development to create a blueprint for the aircraft’s structure, systems, and functionality.
During this stage, aerospace engineers work closely with designers and other experts to define the aircraft’s specifications, performance requirements, and aesthetic aspects. They consider various factors such as aerodynamics, structural integrity, fuel efficiency, and operational capabilities to create an optimal design.
The design and planning stage typically includes:
- Conceptual Design: Engineers and designers create multiple conceptual designs that are evaluated based on their feasibility, performance, and cost-effectiveness. The chosen design becomes the foundation for further development.
- Detailed Design: Once the conceptual design is selected, it is refined, and detailed engineering specifications are created. This includes determining the dimensions, materials, and manufacturing processes for each component of the aircraft.
- Systems Integration: Aircraft are complex machines that require seamless integration of various systems, such as avionics, hydraulics, electrical, and fuel. During this stage, engineers ensure that these systems work harmoniously together.
- Virtual Modeling: Advanced computer-aided design (CAD) software is used to create virtual 3D models of the aircraft. This allows for simulations, analysis, and optimization of different design aspects before proceeding to the manufacturing stage.
- Testing and Validation: Prototypes or scale models are built and subjected to rigorous testing. This helps identify any design flaws or performance issues that need to be addressed before mass production.
The duration of the design and planning stage depends on the complexity of the aircraft, the level of customization, and the efficiency of the design team. It can range from several months to years, especially for large commercial aircraft or military jets that require extensive testing and validation.
Efficient collaboration and communication between design engineers, manufacturers, and suppliers are crucial during this stage to ensure that the design can be successfully translated into a functional aircraft. Any modifications or changes to the design may impact subsequent stages of the construction process, underscoring the importance of thorough planning and design accuracy.
Manufacturing and Assembly Stage
The manufacturing and assembly stage is where the design and planning come to life as the physical components of the aircraft are manufactured and assembled together. This stage is a complex and meticulous process that requires skilled labor, advanced machinery, and strict quality control measures to ensure the integrity and safety of the aircraft.
During this stage, the following steps are typically involved:
- Component Production: Various components of the aircraft, including the fuselage, wings, tail, landing gear, and engine, are manufactured. This involves precise machining, welding, composite layup, and other specialized processes to create parts that meet the design specifications.
- Assembly: Once the individual components are manufactured, they are carefully assembled according to the design specifications. This involves fitting and connecting the different parts together, such as attaching the wings to the fuselage, installing the landing gear, and securing the control surfaces.
- Aircraft Systems Installation: The installation of the aircraft’s systems and subsystems takes place during this stage. This includes the electrical systems, avionics, hydraulics, fuel systems, and other crucial components that make the aircraft operational.
- Interiors: The interior components of the aircraft, such as passenger seats, cabin panels, and lavatories, are installed. This stage may also involve customizations based on customer preferences or specific aircraft configurations.
- Painting and Finishing: Once all the major components are assembled, the aircraft undergoes a painting process where the exterior is painted with the desired colors and livery. The finishing touches, including the installation of logos, registration numbers, and interior decorations, are also done during this stage.
The manufacturing and assembly stage can take several months to years, depending on the complexity of the aircraft, the availability of resources, and the efficiency of the production line. The process requires stringent quality control measures to ensure that each component is manufactured to the highest standards and that the assembly is done with precision.
Efficient coordination between different departments, such as manufacturing, logistics, quality control, and assembly, is essential during this stage to minimize delays and ensure a smooth workflow. Any issues or discrepancies discovered during the manufacturing and assembly stage must be addressed promptly to ensure the aircraft’s integrity and compliance with regulations.
Testing and Certification Stage
The testing and certification stage is a critical phase in the construction of an aircraft. During this stage, the fully assembled aircraft undergoes a series of rigorous tests to ensure its safety, performance, and compliance with industry standards and regulations.
Here are some key aspects of the testing and certification stage:
- Ground Testing: Before the aircraft can take to the skies, it must undergo extensive ground testing. This includes testing the functionality of all systems, conducting structural tests, and performing engine runs to validate performance parameters.
- Flight Testing: Once the ground testing is successfully completed, the aircraft is ready for flight testing. Highly skilled test pilots and engineers perform a series of test flights to evaluate the aircraft’s handling characteristics, stability, and performance in various flight conditions.
- Certification Process: The aircraft must receive certification from regulatory bodies such as the Federal Aviation Administration (FAA) or the European Aviation Safety Agency (EASA). The certification process involves comprehensive assessments of the aircraft’s design, manufacturing, and performance to ensure compliance with safety standards.
- Type Certification: For new aircraft models, achieving type certification is a significant milestone. It demonstrates that the aircraft meets the applicable airworthiness regulations and is authorized for commercial operation.
- Continued Airworthiness: Even after achieving certification, aircraft manufacturers must adhere to the guidelines for continued airworthiness. This includes regular inspections, maintenance, and compliance with manufacturer-recommended service bulletins to ensure ongoing safety and performance.
The testing and certification stage can take several months, sometimes even years, depending on factors such as the complexity of the aircraft, the number of required flight hours for certification, and the regulatory requirements specific to the aircraft’s country of operation.
Thorough testing and certification are crucial to ensuring the safety of the aircraft and the passengers who will fly in it. Any defects or issues discovered during these tests must be addressed and resolved before the aircraft can be considered airworthy.
It’s important to note that the testing and certification stage is not a one-time event. Ongoing monitoring, including rigorous maintenance and periodic inspections, is necessary to ensure the continued airworthiness of the aircraft throughout its operational life.
Customization and Optional Features
One of the factors that can impact the construction time of an aircraft is the level of customization and the inclusion of optional features. Aircraft manufacturers often offer a range of customization options to meet the specific needs and preferences of their customers.
Customization can involve various aspects of the aircraft, including the cabin layout, seating configuration, in-flight entertainment systems, and interior finishes. It allows customers to personalize the aircraft to suit their unique requirements, whether it’s for corporate use, luxury travel, or specialized missions.
Here are some key points to consider with regards to customization and optional features:
- Cabin Layout: Customers can choose from different cabin layout options to accommodate their specific needs, such as the number of passengers, galley placement, and lavatory arrangements.
- Seating Configuration: The seating arrangement and design can be tailored to provide optimal comfort and functionality. Options include different seat configurations, seat materials, and additional amenities like lie-flat beds or conference seating areas.
- Avionics and Entertainment Systems: Advanced avionics and in-flight entertainment systems can be customized to meet the customer’s preferences. This may include high-definition video screens, wireless connectivity, and custom control interfaces.
- Interior Finishes: Customers can select from a range of finishes, including premium materials, upholstery, decorative elements, and lighting options to create a luxurious and visually appealing cabin environment.
- Specialized Equipment and Features: Some customers may require specialized equipment or features based on their intended use of the aircraft. This could include medical equipment, surveillance systems, or additional fuel tanks for extended range capabilities.
While customization allows for a more personalized and tailored aircraft, it can add to the overall construction time. Each customization option requires careful planning, engineering, and integration into the final design. Additionally, the inclusion of optional features may involve additional manufacturing and installation processes, which can extend the construction timeline.
Efficient communication and collaboration between the customer, aircraft manufacturer, and suppliers are vital during the customization phase to ensure that the customer’s requirements are met while considering the impact on construction time.
Ultimately, the balance between customization and construction time depends on the customer’s priorities and the complexity of the requested modifications. Manufacturers strive to deliver high-quality customized aircraft within an agreed-upon timeframe, balancing the desire for personalization with the need for efficient production and certification processes.
Industry Standards and Regulations
The aircraft manufacturing industry operates under strict standards and regulations to ensure the safety, reliability, and airworthiness of aircraft. Compliance with these standards and regulations is a crucial aspect of the construction process and can significantly impact the timeline.
Here are some key points to consider regarding industry standards and regulations:
- Certification Requirements: Aircraft must undergo a rigorous certification process to demonstrate their compliance with airworthiness standards set by regulatory authorities such as the Federal Aviation Administration (FAA) or the European Aviation Safety Agency (EASA). The certification process includes a thorough evaluation of the aircraft’s design, materials, systems, and performance.
- Structural Requirements: Aircraft must meet specific structural requirements to ensure strength, durability, and resistance to various operating conditions, including atmospheric pressure, temperature changes, and aerodynamic forces.
- Systems Integrity: The aircraft’s systems, including electrical, hydraulic, and fuel systems, must adhere to strict standards to ensure they operate safely and reliably. These standards cover aspects such as wiring, connectors, power supply, and system redundancy.
- Avionics Compliance: Avionics systems, including communication, navigation, and surveillance equipment, must comply with industry standards to ensure proper operation, accuracy, and compatibility with air traffic control systems.
- Manufacturing Standards: The manufacturing processes used to produce aircraft components must comply with standards to ensure consistency, quality, and traceability. These standards cover areas such as material selection, machining, fabrication, and assembly techniques.
- Maintenance and Airworthiness: Ongoing airworthiness and maintenance requirements must be followed to ensure the continued safe operation of the aircraft throughout its lifecycle. This includes regular inspections, maintenance tasks, and compliance with manufacturer-recommended service bulletins.
Complying with industry standards and regulations requires careful planning, documentation, and verification throughout the construction process, which can add time to the overall timeline. However, adherence to these standards is critical for ensuring the safety and airworthiness of the aircraft.
Manufacturers work closely with regulatory authorities and certification agencies to navigate the certification process efficiently. Close collaboration with engineers, quality control personnel, and regulatory experts is essential to ensure that the construction process aligns with the necessary requirements.
It’s worth noting that industry standards and regulations are continuously evolving to address emerging technologies, environmental considerations, and safety enhancements. Keeping up with these changes and incorporating them into the construction process is an ongoing commitment for manufacturers.
Collaboration with Suppliers and Contractors
Collaboration with suppliers and contractors is a vital aspect of aircraft construction. The successful completion of an aircraft project relies on efficient coordination, effective communication, and a reliable supply chain. Collaboration with suppliers and contractors can significantly impact the construction time and overall success of the project.
Here are some key points to consider regarding collaboration with suppliers and contractors:
- Component Sourcing: Aircraft manufacturers rely on a network of suppliers to provide various components and subsystems. The collaboration with suppliers starts early in the process, ensuring that the required components are available when needed. This collaboration includes establishing quality standards, verifying certifications, and clarifying technical specifications.
- Contract Negotiation: Collaboration often involves negotiating contracts with suppliers and contractors. These contracts define expectations, pricing, delivery schedules, and quality standards. Clear and well-negotiated contracts ensure smooth collaboration and minimize potential delays or discrepancies.
- Timeline Management: Effective collaboration ensures that suppliers and contractors are aware of the project timeline and can deliver components or perform services within the specified timeframe. Regular communication and coordination are essential to stay on track and address any potential delays or issues promptly.
- Quality Assurance: Collaboration involves establishing quality control measures and inspection protocols with suppliers and contractors. These measures ensure that the components or services provided meet the required standards and specifications. Regular audits and quality checks help maintain consistency and reliability throughout the construction process.
- Technical Support: Suppliers and contractors often provide technical support, such as assisting with installation, troubleshooting, or resolving any issues that may arise during the construction process. Collaborative relationships with suppliers ensure quick and effective resolution of technical challenges.
- Continuous Improvement: Collaborating with suppliers and contractors enables feedback and exchange of knowledge. By establishing open lines of communication and fostering a collaborative environment, manufacturers can benefit from supplier expertise and drive continuous improvement in the construction process.
Efficient collaboration with suppliers and contractors requires effective project management and clear communication channels. Establishing strong relationships and ensuring transparency between all parties involved in the construction process can help identify and address potential challenges proactively.
Manufacturers often work on cultivating long-term relationships with reliable suppliers to create a stable supply chain. Such collaboration fosters trust, promotes efficiency, and minimizes potential disruptions during the construction of the aircraft.
Experience and Efficiency of the Aircraft Manufacturer
The experience and efficiency of the aircraft manufacturer play a critical role in the construction time of an aircraft. Manufacturers with a proven track record and extensive industry experience are often able to streamline the construction process, optimize workflows, and deliver aircraft in a timely manner.
Here are some key points to consider regarding the experience and efficiency of the aircraft manufacturer:
- Production Processes: Experienced manufacturers have well-established production processes that have been refined over time. These processes ensure effective utilization of resources, reduce waste, and improve overall efficiency. Manufacturers with efficient production processes can consistently meet construction timelines.
- Skilled Workforce: The expertise and skills of the workforce significantly contribute to the efficiency of the construction process. Experienced manufacturers often employ highly skilled and trained engineers, technicians, and craftsmen who are proficient in their respective areas. Their expertise helps in efficiently executing tasks, minimizing errors, and meeting construction timelines.
- Supplier Relationships: Established manufacturers often have long-standing relationships with suppliers, which leads to better collaboration, timely delivery of components, and reliable access to necessary resources. Inefficient supply chain management can cause delays and disruptions in the construction process. However, experienced manufacturers are adept at managing relationships with suppliers to ensure smooth operations.
- Quality Control Measures: Experienced manufacturers have well-defined quality control measures in place, ensuring that each step of the construction process meets rigorous standards. These measures help in identifying and rectifying any issues promptly, resulting in a smoother and more efficient construction timeline.
- Process Optimization: Over time, experienced manufacturers have honed their construction processes through careful analysis, evaluation, and continuous improvement initiatives. They identify areas for optimization, implement innovative techniques, and adopt industry best practices to enhance efficiency and reduce construction time.
- Planning and Project Management: Experienced manufacturers have a thorough understanding of the intricacies involved in aircraft construction. They are proficient in planning and project management, developing realistic timelines, and effectively allocating resources. This ensures that construction progresses smoothly and is completed in a timely manner.
While the experience and efficiency of the aircraft manufacturer are important factors, it’s essential to note that construction time can still vary depending on other factors such as aircraft complexity, customization requirements, and certification processes. Collaboration with suppliers, effective project management, and adherence to industry standards collectively contribute to the overall construction timeline.
Customers often prioritize working with experienced and reputable manufacturers due to their ability to deliver aircraft efficiently, meet deadlines, and provide high-quality products. The experience and expertise of the manufacturer instill confidence in customers and contribute to the successful completion of the aircraft construction process.
Breakdown of Time in Different Aircraft Types
The construction time of an aircraft can vary depending on the type and complexity of the aircraft. Different aircraft types have unique design requirements, manufacturing processes, and certification procedures, resulting in varying construction timelines. Here is a breakdown of the time involved in constructing different aircraft types:
- Small General Aviation Aircraft: Small general aviation aircraft, such as single-engine piston aircraft or light sport aircraft, tend to have relatively shorter construction times. Building these aircraft typically takes several months to a year. Their simpler design, smaller size, and fewer complex systems contribute to quicker construction timelines.
- Regional and Business Jets: Regional and business jets, which include aircraft like the Bombardier Challenger and Embraer Phenom, are more complex than small general aviation aircraft. The construction time for these aircraft can range from 1 to 3 years. They require advanced systems integration, higher levels of customization, and rigorous testing and certification processes.
- Commercial Airliners: Commercial airliners are the most complex and time-consuming aircraft to build and certify. These large aircraft, such as the Boeing 737 or Airbus A320, typically take several years to complete. The construction time can vary depending on the specific model and the level of customization required by the airline. Additionally, the rigorous certification process, which includes extensive flight testing and adherence to strict industry regulations, contributes to the longer construction timeline.
- Military Aircraft: Military aircraft, such as fighter jets or transport aircraft, are highly specialized and often have unique design requirements. The construction time for military aircraft can vary significantly, depending on factors like complexity, technology integration, and specific mission capabilities. Building some military aircraft can take several years due to their advanced features and the stringent certification process required in the defense sector.
It’s important to note that these construction times are approximate, and actual timelines can vary based on various factors, including manufacturer efficiency, supply chain management, customer requirements, and unforeseen circumstances. Advanced planning, effective project management, and collaboration with suppliers and contractors are critical in achieving timely delivery without compromising safety or quality.
Furthermore, it’s worth mentioning that these timelines primarily refer to the construction phase itself and do not account for the entire aircraft development process, which includes the design, testing, certification, and delivery stages.
Regardless of the aircraft type, manufacturers strive to balance construction time with high-quality craftsmanship and compliance with industry standards. The goal is to deliver reliable and safe aircraft within a reasonable timeframe, meeting the specific requirements of each customer and industry segment.
Conclusion
Building an airplane is a complex and intricate process that involves multiple stages, meticulous planning, and adherence to industry standards and regulations. The time it takes to construct an aircraft can vary depending on several factors, including the type of aircraft, the level of customization, the efficiency of the manufacturer, and collaboration with suppliers and contractors.
The design and planning stage sets the foundation for the entire construction process, involving conceptual design, detailed engineering, and systems integration. The manufacturing and assembly stage sees the physical components being produced and assembled together, with meticulous attention to quality control and precision. The testing and certification stage ensures the aircraft’s safety, performance, and compliance through rigorous ground and flight tests, and certification from relevant regulatory bodies.
Factors such as customization and optional features, industry standards and regulations, collaboration with suppliers and contractors, and the experience and efficiency of the manufacturer can all impact the construction time. The level of customization required, the need to comply with evolving regulations, efficient collaboration with suppliers, and the experience of the manufacturer all play crucial roles in determining the timeline.
Additionally, construction time can vary depending on the type of aircraft. Small general aviation aircraft typically have shorter construction times, while commercial airliners and military aircraft can take several years due to their complexity and rigorous certification requirements.
In conclusion, constructing an aircraft requires a well-coordinated effort from a team of experts, precise planning, and efficient execution. Aircraft manufacturers strive to deliver high-quality aircraft within reasonable timelines while ensuring compliance with industry standards and regulations. By managing various factors effectively, aircraft manufacturers can meet customer expectations, provide safe and reliable aircraft, and contribute to the advancement of aviation technology.